Cómo Delfos se anticipa a los fallos de los rodamientos principales de los aerogeneradores con Machine Learning
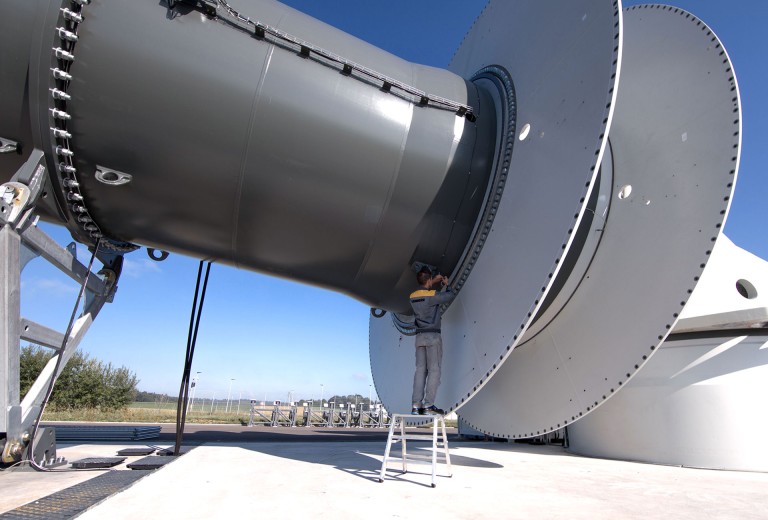
Estas fallas no solo son costosas, sino que también mantienen los activos fuera de línea durante períodos prolongados. Teniendo esto en cuenta, el equipo de Delfos desarrolló una metodología innovadora para predecir este tipo de fallos con meses de antelación y con una precisión impresionante.
El desafío: predecir las fallas críticas antes de que se conviertan en un problema
Rodamientos principales en turbinas sufren desgaste por fatiga y, cuando fallan, las reparaciones son costosas y llevan mucho tiempo. Detectar las primeras señales de estas fallas utilizando únicamente datos SCADA (datos operativos del parque eólico) siempre ha sido un desafío, hasta ahora.
Delfos creó una red neuronal (MLP — Multilayer Perceptron) que predice la temperatura esperada del rodamiento principal. Cuando la temperatura real comienza a desviarse con frecuencia del valor esperado, el sistema emite una alerta. Puede parecer sencillo, pero el proceso subyacente es muy sofisticado.
La innovación: modelo validado en una flota real
Esta metodología se aplicó durante 2,5 años 155 turbinas eólicas con una potencia nominal de 2,5 MW. Los modelos se entrenaron individualmente para cada turbina utilizando datos recopilados cada 10 minutos. Además, el equipo tuvo acceso a órdenes de trabajo y registros de mantenimiento, lo que les permitió validar las alertas comparándolas con datos del mundo real.
El análisis de rendimiento es impresionante:
- 100% de recuperación: No se detectó ningún fallo real.
- Precisión del 95%: Casi todas las alertas emitidas eran precisas.
- Puntuación F1 del 97,5%: Un equilibrio casi perfecto entre precisión y cobertura.
Resultados que afectan a las operaciones
Entre las alertas verdaderas, El 83% estaba relacionado con fallos en los rodamientos principales inducidos por la fatiga. En un caso, Delfos pudo predecir el problema 111 días antes se activó la primera alarma SCADA.
Además de anticipar las fallas, el sistema también detectó aumentos de temperatura cercanos a eventos de mantenimiento programados, lo que sugiere que factores como el calentamiento de la góndola también pueden interferir con las condiciones de los componentes.
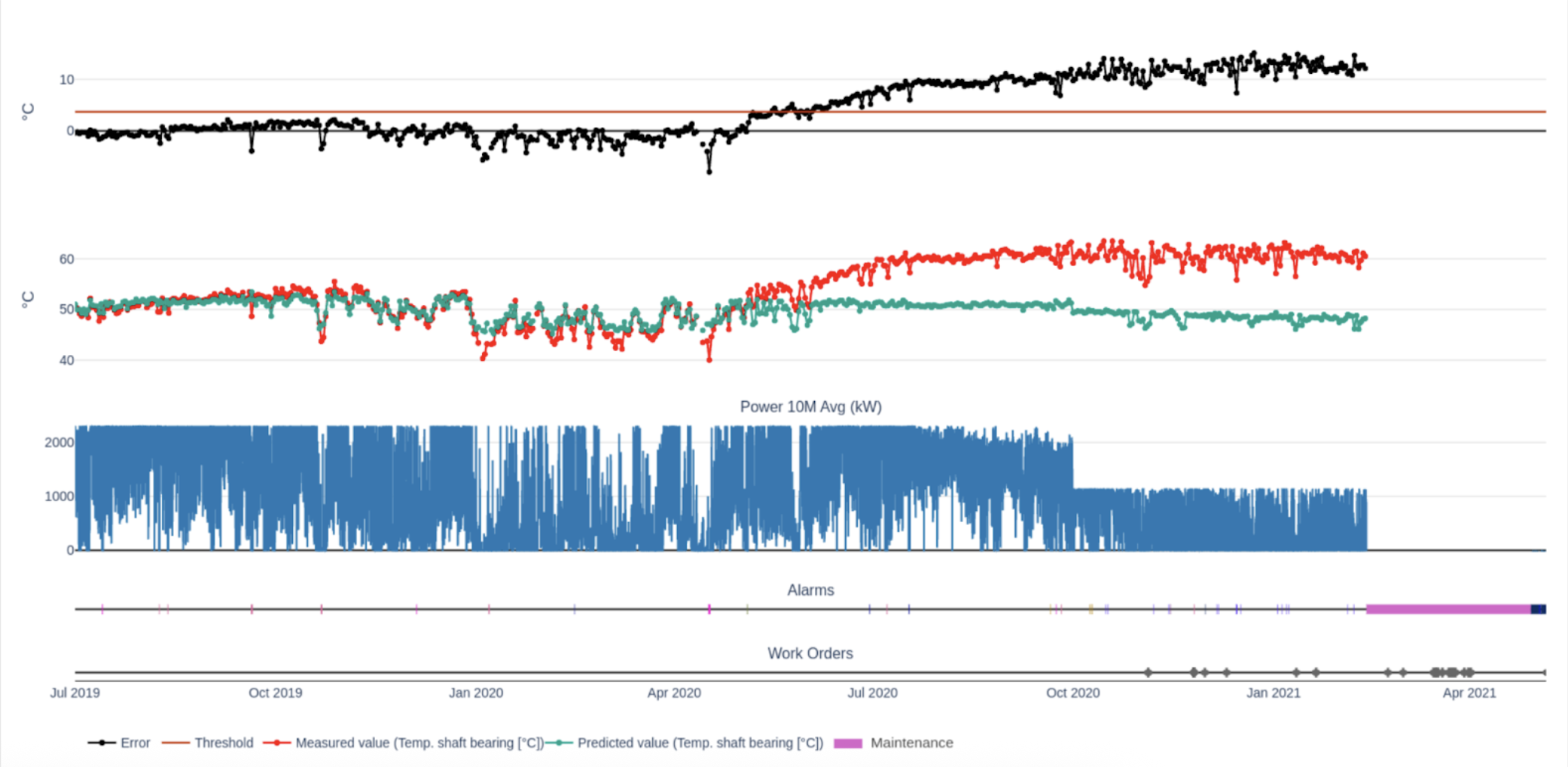
¿Por qué importa esto?
Con un sistema como este:
- Puede planificar las intervenciones con antelación.
- Se reduce el tiempo de inactividad de la turbina.
- Se evita el mantenimiento innecesario, lo que reduce los costos.
- Las decisiones operativas se toman con mayor confianza.
Aprendizajes clave
- El aprendizaje automático por sí solo no es suficiente: Bien documentado mantenimiento los registros son esenciales.
- Es posible que el SCADA no sea suficiente: Los modelos predictivos pueden identificar las fallas antes que las alarmas estándar.
- No todos los calefactores indican un fallo: El contexto operativo importa, y mucho.
Conclusión
La investigación de Delfos demuestra que es posible escalar una metodología de predicción de fallas en un rodamiento principal con una confiabilidad muy alta. La integración del aprendizaje automático, los datos de SCADA y la validación mediante órdenes de trabajo sitúa a Delfos a la vanguardia del mantenimiento predictivo de la energía renovable.
¿Dónde se publicó esto?
Este estudio se presentó a Wind Europe 2025, una de las principales conferencias sobre energía eólica de Europa, a cargo del equipo de investigación de Delfos Energy.
Para acceder al estudio completo y al contenido enriquecido, complete el siguiente formulario:
Reserva una reunión
Conectemos y forjemos nuevas asociaciones
Custom Renewable Energy Solutions
Póngase en contacto con nosotros hoy mismo para hablar sobre sus necesidades de energía renovable y encontrar la solución perfecta para su empresa.