How Delfos Is Anticipating Main Bearing Failures in Wind Turbines Using Machine Learning
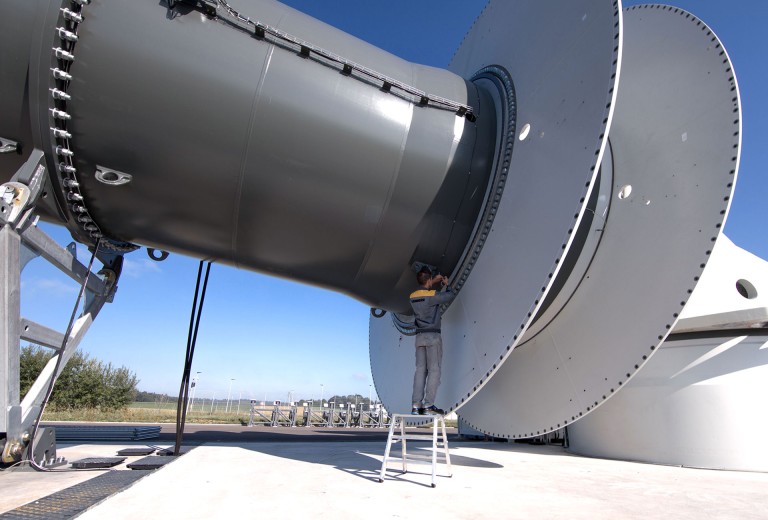
These failures are not only costly but also keep assets offline for extended periods. With this in mind, the Delfos team developed an innovative methodology to predict this type of failure months in advance — and with impressive accuracy.
The Challenge: Predict Critical Failures Before They Become a Problem
Main bearings in turbines suffer from fatigue wear, and when they fail, repairs are expensive and time-consuming. Detecting early signs of these failures using only SCADA data (operational data from the wind farm) has always been a challenge — until now.
Delfos created a neural network (MLP – Multilayer Perceptron) that predicts the expected temperature of the main bearing. When the actual temperature starts to deviate frequently from the expected value, the system issues an alert. It may sound simple, but the process behind it is highly sophisticated.
The Innovation: Model Validated on a Real Fleet
This methodology was applied over 2.5 years on 155 wind turbines rated at 2.X MW. The models were individually trained for each turbine using data collected every 10 minutes. Additionally, the team had access to work orders and maintenance records, which allowed them to validate alerts against real-world data.
The performance analysis is impressive:
- 100% Recall: No actual failure went undetected.
- 95% Precision: Almost all issued alerts were accurate.
- F1-Score of 97.5%: An almost perfect balance between precision and coverage.
Results That Impact Operations
Among the true alerts, 83% were related to fatigue-induced main bearing failures. In one case, Delfos was able to predict the problem 111 days before the first SCADA alarm was triggered.
Beyond anticipating failures, the system also detected temperature increases close to scheduled maintenance events, suggesting that factors like nacelle heating may also interfere with component conditions.
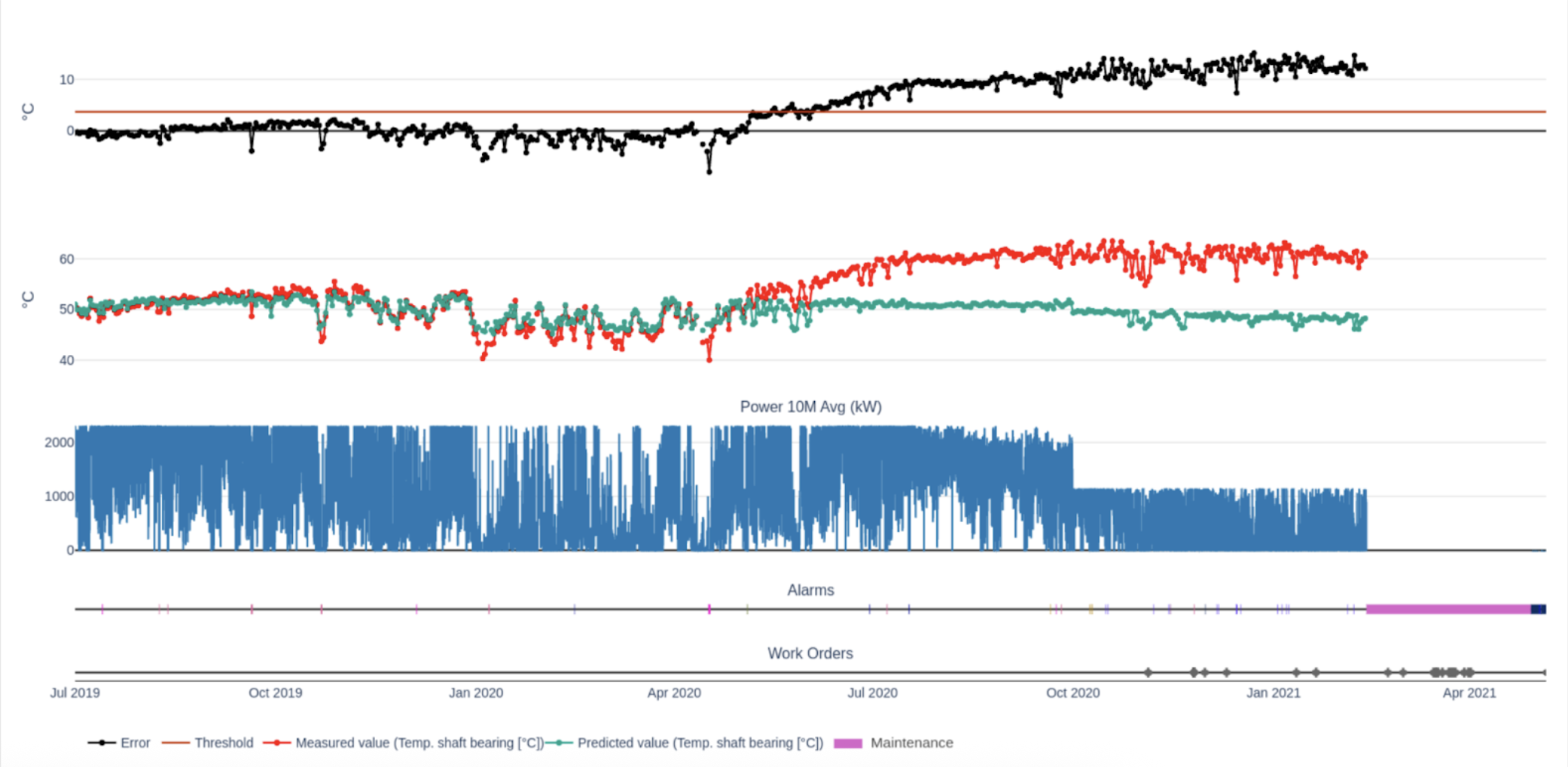
Why Does This Matter?
With a system like this:
- You can plan interventions in advance.
- Turbine downtime is reduced.
- Unnecessary maintenance is avoided, reducing costs.
- Operational decisions are made with greater confidence.
Key Learnings
- Machine Learning alone is not enough: Well-documented maintenance records are essential.
- SCADA may not be sufficient: Predictive models can identify failures before standard alarms.
- Not all heating indicates failure: Operational context matters — a lot.
Conclusion
Delfos' research demonstrates that it is possible to scale a main bearing fault prediction methodology with very high reliability. The integration of Machine Learning, SCADA data, and validation using work orders positions Delfos at the forefront of predictive maintenance for renewable energy.
Where Was This Published?
This study was submitted to Wind Europe 2025, one of the leading wind energy conferences in Europe, by the Delfos Energy research team.
To access the full study and rich content, fill in the form below:
Book a meeting
Let's connect and forge new partnerships
Custom Renewable Energy Solutions
Contact us today to discuss your renewable energy needs and find the perfect solution for your business.