Predictive Maintenance: Anticipating failures and expanding results
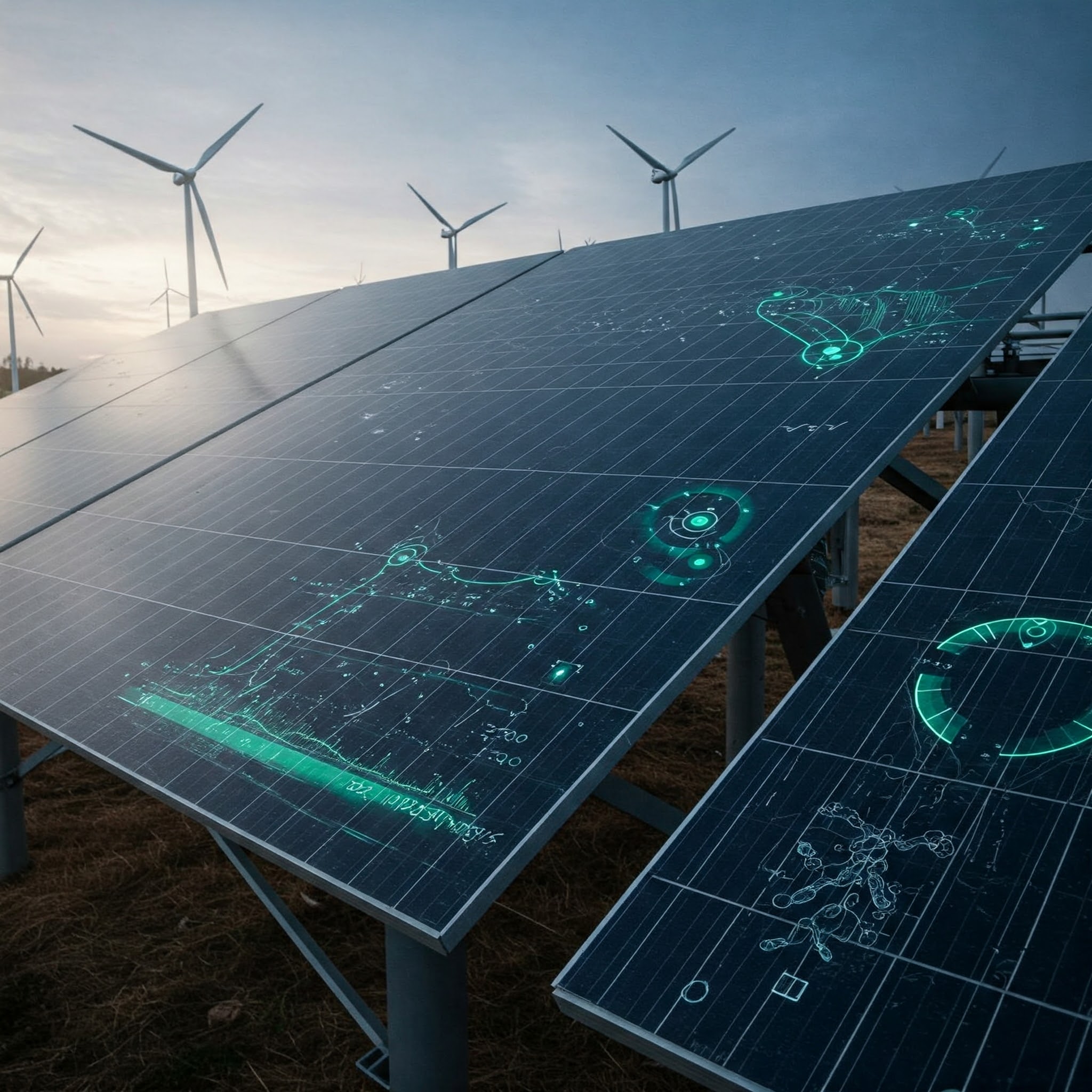
The global energy transformation is advancing at a rapid pace, and ensuring high performance of solar and wind power plants is more strategic than ever. In this scenario, predictive maintenance emerges as an essential ally for those who want to reduce costs, avoid unexpected failures, and maximize asset lifespan.
But after all, what is predictive maintenance? And how does it differ from corrective and preventive maintenance? Let’s explore these answers and understand how technologies like Delfos' are redefining the future of renewable asset management.
What is Predictive Maintenance?
Predictive maintenance is a strategy that uses operational data and intelligent algorithms to predict failures before they happen. Instead of waiting for a component to break (corrective maintenance) or performing replacements at fixed intervals (preventive maintenance), predictive maintenance identifies anomalies and signs of wear in advance, based on the actual behavior of the equipment.
In practice, it's like giving your asset a technological “crystal ball,” using sensors, machine learning, and artificial intelligence to detect any pattern deviation that could indicate a future failure.
Predictive, Corrective and Preventive Maintenance: Understand the Differences
Corrective Maintenance: occurs after the failure. It is reactive and generally involves high repair costs and long downtime.
Preventive Maintenance: is performed on a scheduled basis, based on time or equipment usage, regardless of their actual condition.
Predictive Maintenance: is based on continuous monitoring and predictive analysis, allowing intervention only when there are concrete signs of degradation.
Companies that adopt predictive maintenance can drastically reduce unplanned failures, optimize O&M resource allocation, and maximize asset operational availability.
Types of Predictive Maintenance
There are several approaches and technologies applied to predictive maintenance, including:
- Vibration Analysis: used to detect mechanical failures in rotating components, such as bearings and gears.
- Thermography: identifies abnormal heating points, essential for monitoring solar panels, inverters, and transformers.
- Condition Monitoring: collects sensor data (such as temperature, pressure, current) to detect operational deviations.
- Machine Learning and AI: models the "healthy" behavior of assets and automatically identifies failure patterns.
- Advanced Statistical Analyses: segments data to detect degradation trends and behavior changes.
Delfos, for example, combines all these approaches, offering a robust Intelligent APM (Asset Performance Management) platform capable of detecting failures up to 320 days in advance.
Failure Detection up to 320 Days in Advance: Understand How Delfos Does It
Delfos has developed an advanced predictive analysis system that combines:
- Machine learning models specific to each component (e.g., main bearings, generators, gearboxes, solar inverters).
- Continuous monitoring of operational time series (such as temperature, vibration, electric current, and pressure).
- Automatic detection of subtle deviations from the expected healthy behavior of each asset.
With this methodology, Delfos has identified, in real cases, failures in critical components such as main wind turbine bearings and solar inverters, with up to 320 days of lead time before the critical event occurred.
This early detection is made possible thanks to:
- Proprietary AI-based prediction models (Delfos Gen™).
- Ability to learn the “normal” behavior of the asset in different weather and operational conditions.
- Application of intelligent thresholds (dynamic limits) that consider seasonality and operating patterns, avoiding false positives.
Example of Predictive Maintenance in Practice
Imagine a wind turbine: one of the most critical components is the main bearing, which supports the entire load of the blades. With Delfos’ predictive maintenance, sensors continuously monitor the component’s temperature, vibration, and speed.
Upon identifying a slight abnormal temperature increase, even within operational limits, the system generates a predictive alert. With this data in hand, the O&M team can schedule inspection and bearing replacement before it fails, preventing unexpected downtime and saving millions in repair costs and revenue loss.
In solar energy, Delfos also stands out with intelligent monitoring solutions for pyranometers, essential for ensuring the accuracy of solar irradiance measurement and detecting sensor drift.
How Delfos Raises the Predictive Maintenance Standard
The Delfos platform goes beyond simple data collection:
- Monitors over 14 GW of renewable assets.
- Uses 100+ performance algorithms for different types of assets and components.
- Generates actionable predictive insights, supporting strategic decision-making.
In addition, Delfos offers reports, smart visualization dashboards, and continuously updated machine learning models to reflect changes in asset behavior.
The Future is Predictive
Predictive maintenance represents a turning point in wind and solar plant management. With the right technology, such as the one offered by Delfos, it’s possible to increase operational efficiency, reduce downtime, and turn data into competitive advantage.Want to know how Delfos can revolutionize the management of your assets?
👉 Talk to our specialists and discover how to take your renewable operation to the next level.
Book a meeting
Let's connect and forge new partnerships
Custom Renewable Energy Solutions
Contact us today to discuss your renewable energy needs and find the perfect solution for your business.