Predictive, Corrective and Preventive Maintenance: How to Choose the Ideal Strategy for Your Renewable Assets
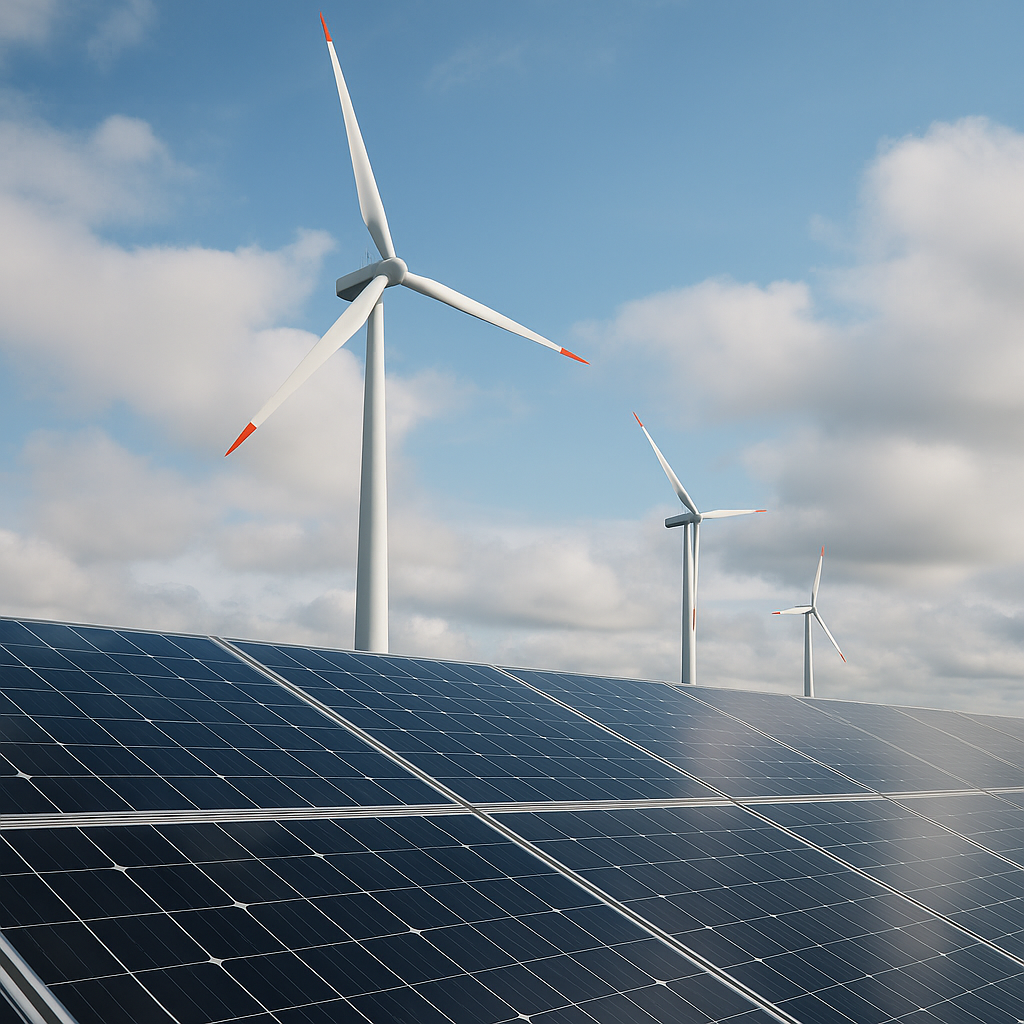
This content is especially useful for O&M managers and coordinators looking to increase operational availability, prevent critical failures, and improve the performance of solar or wind farms with greater intelligence and predictability. Here, we clearly explain the differences between the three types of maintenance and show how Delfos' predictive technology is transforming the daily routine of energy operations.
Understanding the Three Types of Maintenance
In the energy sector, maintenance is not just a fixed cost. It is a strategic decision that directly impacts asset generation and revenue.
Corrective maintenance is the most reactive. It takes place after the problem has already caused downtime, energy loss or equipment damage. It may be unavoidable at times, but relying on it as your primary approach is like driving while looking in the rearview mirror.
Preventive maintenance tries to act before the failure, using scheduled inspections and replacements. While safer than corrective, it still carries inefficiencies such as parts replaced too early, poorly allocated man-hours and unnecessary shutdowns.
Predictive maintenance emerges as the natural evolution. Based on real operational data and AI algorithms, it identifies abnormal patterns and forecasts failures in advance. This allows interventions to be scheduled at the right time, not too early and not too late.
Why This Decision Matters for Your Operation
The way your team handles maintenance directly impacts critical KPIs like operational availability, capacity factor and energy efficiency. In renewable assets, undetected failures result not only in repair costs but primarily in ungenerated and unrecoverable energy revenue.
In one of Delfos' most relevant cases, applying a predictive model to a wind turbine enabled early detection of failures in the yaw system, avoiding the loss of 7,778 MWh over 299 days and significantly reducing maintenance costs. This preventive action was key to preserving asset performance and ensuring greater operational predictability. The full case study is available here.
In the solar sector, Delfos identified intermittent failures in string box cables that were silently impacting energy generation. Thanks to early detection and AI-guided correction, 681 MWh of energy were recovered, showing how small hidden failures can lead to major losses when not addressed intelligently. The full case is available at this link.
These numbers are not estimates. They are documented results from real operations. They show what is at stake when maintenance shifts from a reactive cost to a data-driven strategic decision.
AI in Action: How Predictive Maintenance Works at Delfos
Delfos' platform combines machine learning, SCADA data, failure histories and weather conditions to monitor each asset in real time. It learns standard behavior and flags potentially critical deviations long before failures occur.
In practice, this means proven results:
In Delfos' internal studies, failures were predicted up to 299 days in advance, with anomalies identified in components like main bearings and solar inverters.
Performance analysis showed up to 30% reduction in O&M costs when comparing operations with and without AI between 2022 and 2024.
In real cases with more than 100 monitored turbines, the platform helped avoid up to 500 MWh per turbine per month through predictive alerts that kept equipment performing at optimal levels.
More than just software, Delfos delivers a new operational model. Decisions are based on data, field teams act preventively and asset performance is tracked with precision, bringing real gains to your operation.
Hybrid Strategy: What O&M Leaders Are Doing
The most efficient trend in the sector today is combining all three approaches, with predictive maintenance as the strategic core.
Corrective maintenance becomes the exception, used only for unavoidable or external failures.
Preventive maintenance remains useful but becomes more targeted based on predictive insights, reducing waste.
Predictive maintenance, powered by AI, stands as the operational pillar, enabling proactive, auditable and data-driven management.
This model is already being adopted by industry leaders. It delivers not only operational gains but also strengthens governance and regulatory compliance, especially in a landscape with increasing demands for traceability and energy-financial control.
The Future Belongs to Those Who Anticipate
Predictive maintenance marks a paradigm shift in energy asset management. More than reducing failures, it helps build more resilient, cost-effective operations ready for the challenges of a constantly evolving sector.
If you're ready to move beyond guesswork and static spreadsheets and start making decisions based on real data and automated insights, now is the time to make the shift.
Let’s talk
Reach out to the Delfos team and learn how to apply AI-powered predictive maintenance to your operation. We will show you, using your own data, where your biggest improvement opportunities lie and what they are worth.
Book a meeting
Let's connect and forge new partnerships
Custom Renewable Energy Solutions
Contact us today to discuss your renewable energy needs and find the perfect solution for your business.