Using AI to detect faults in the pitch system and avoid losses of USD20,000 per turbine
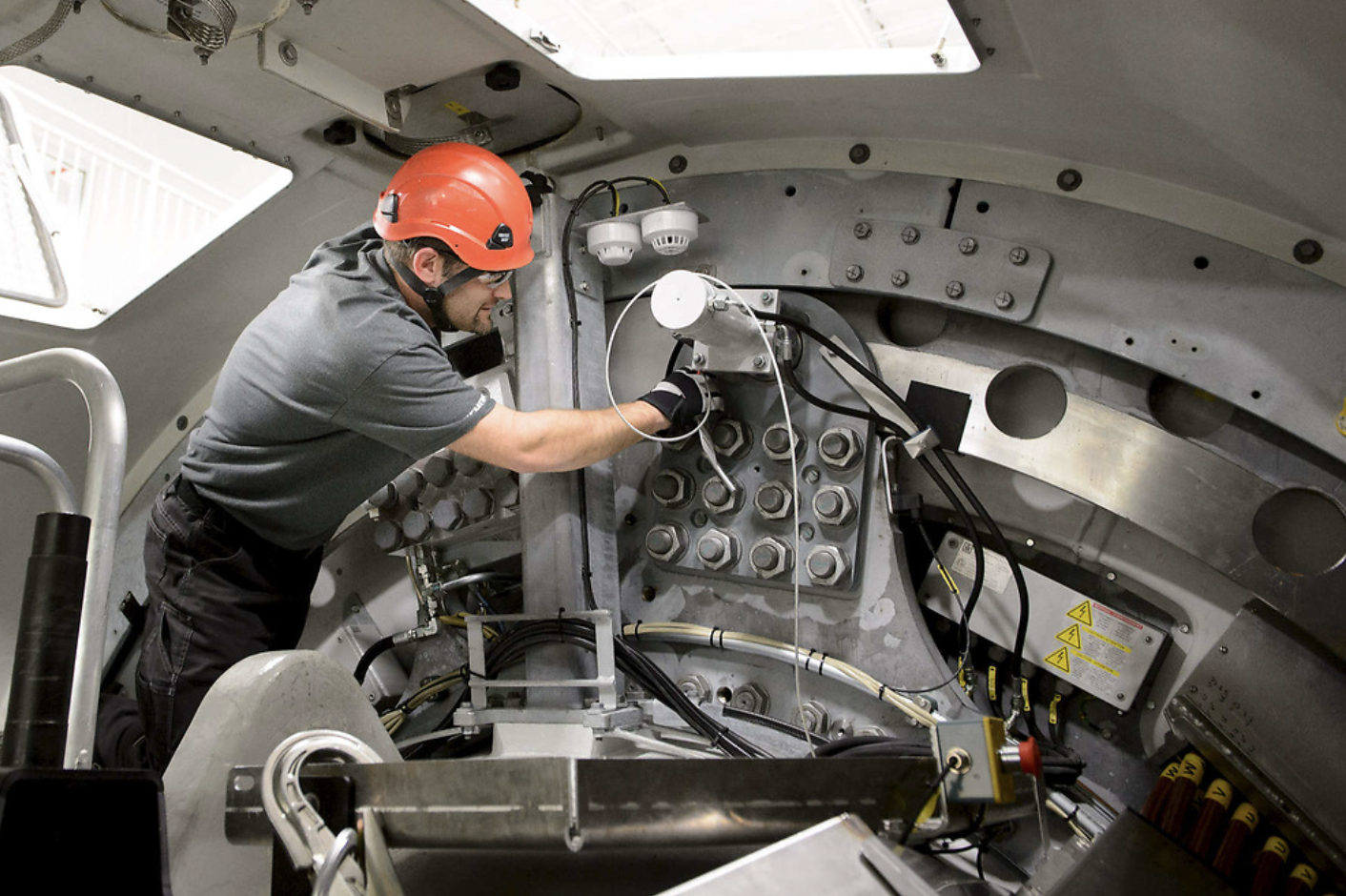
Did you know that a fault in the pitch system - responsible for adjusting the angle of wind turbine blades - can significantly reduce the energy output of a wind turbine, without anyone noticing straight away? This is exactly the challenge that the Delfos team faced and solved with an innovative approach based on SCADA data and machine learning models.
The study shows how it is possible to identify these faults early on and quantify their impact on energy generation - with the potential to avoid losses of more than USD20,000 per year per turbine (+329.7 MWh in the AEP).
The problem: when the pitch system compromises generation
In variable speed turbines, the pitch system is essential for two functions:
- Optimize energy production by adjusting the angle of the blades according to the wind speed.
- Protect the equipment in extreme conditions.
But this system doesn't always work perfectly. Often, a fault doesn't bring the wind turbine to a standstill - it just makes it operate less than optimally. The result? A drop in performance that is difficult to notice, but costly.
The solution: artificial intelligence to monitor the unexpected
Delfos has developed an automated pipeline that combines two models:
- Gaussian process with heteroscedasticity, which learns the normal behavior between wind speed and pitch angle for each turbine model.
- Artificial Neural Network (ANN), which validates the data from the nacelle anemometer, ensuring that the pitch alarm is not caused by a wind measurement error.
If a real anomaly in the pitch system is confirmed, the methodology estimates the direct impact on annual production based on the IEC 61400-12-2 standard, simulating the wind turbine's power curve.
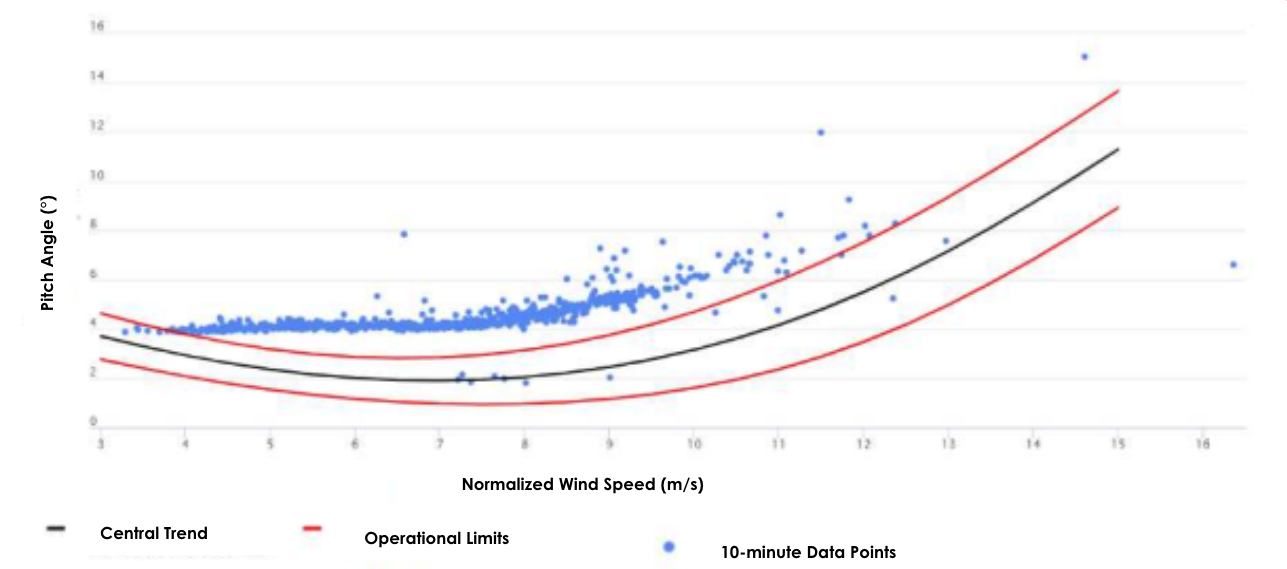
Results that speak for themselves
Two real cases have shown the power of this approach:
Case WTG1 - Pitch anomaly
- Diagnosis: anomalous behavior confirmed by the model.
- Intervention: correction to actuators and software.
- Result: 5.47% gain in AEP, equivalent to +329.7 MWh per year or around USD20,000 in avoided revenue.
Case WTG2 - Anemometer error
- Diagnosis: the pitch alarm was caused by a wind measurement error.
- Intervention: correction to the wind sensor.
- Result: normalization of the models and reliable performance KPIs again.
Why does this matter to the sector?
In addition to preventing financial losses, this methodology brings agility to maintenance, confidence in performance indicators and standardization of analyses even in turbines from different manufacturers. And the best part: with data that already exists in SCADA.
Conclusion: AI in practice creates value
This is yet another example of how Delfos is at the forefront of predictive maintenance in wind energy. By transforming data into actionable insights, we prevent losses, improve efficiency and support evidence-based decisions.
Want to learn more about how this methodology can be applied to your wind farm? Talk to our experts or read the full article presented at Brazil WindPower 2022 by filling in the form below.
Study presented by Nathianne Andrade at the Brazil WindPower 2022 conference.
Book a meeting
Let's connect and forge new partnerships
Custom Renewable Energy Solutions
Contact us today to discuss your renewable energy needs and find the perfect solution for your business.